(The long-promised update. I had intended to take update photographs of the adaptor previously bitched about, but had no decent working camera for a while. Now I have camera and two adaptors worth a gripe, so here goes.)
This happened over the last 48 hours.

In 2013, after a long spell of financial difficulty during which it wasn’t an option, I replaced my laptop’s sadly deteriorated MagSafe [1] power adaptor. That adaptor (Nº2) went up on a high shelf in the interim. And the new adaptor (Nº4) was good. But early this year I noticed the onset of the same deterioration. I might have blogged about it all the way through, but the last few months have been intense . . .
The progressive deterioration whilst in normal use of the new (c.2011 and on) cable for these adaptors seems to go like this:
- The plasticiser in the insulator begins to migrate. This (and its consequences) is more severe towards the laptop end of the cable. Probably responding to heat from the laptop itself. (Today, Nº4’s cable is still quite fresh and hard towards the adaptor end. However, yellowing and softness is detectable about halfway along.)
- The sheath softens and loosens, and you can feel it moving over the conductors below. (The cable is coaxial, with a layer of ground wires round the inner insulator.)
- Boron (I assume) begins to migrate to the surface, i.e. the sheath yellows. It is likely that the plasticiser is beginning to leach out of the surface in small quantities and is being wiped away in normal handling, and against all the surfaces it contacts.
- The process continues. Assuming that Apple didn’t deliberately coat the ground wires with green gunk [2], the plasticiser combines with copper from the wires and eventually the outer sheath acquires a visible green tinge at the point of greatest stress. (There are always mechanical stresses near a plug; as this sheath softens it also expands, creating extra stress in that area, but the major disruptive influence in the early stages is probably heat. The cable is usually warm to the touch, sometimes very warm, near the plug.)
- The sheath develops a stronger green tinge at the point of maximum stress and begins to wrinkle. Within days, the wrinkle splits. If left to itself, it will continue to expand by an inch or two, splitting at the break as it goes. The ground conductor is now exposed, and there will be some green coppery grease making a mess of everything it touches.
The time this takes may vary, probably depending in the early stages on frequency of use and temperature levels.
I do not know what plasticiser is used in either the older or newer sheaths, though I understand that when this type of problem was first observed in electrical cables in the 1960s (and resolved in the 1970s), the problem plasticisers were lightweight phthalates, which can combine with copper from the cables forming copper phthalate compounds, which appear to be somewhat toxic. I’d like to think that was not the case here, but have no means of testing. Some but not all phthalate plasticisers have been banned in different parts of the world. [α]
The source of the migrating plasticiser here may actually be the inner insulator. If the outer sheath has (by design or accident) a lower concentration of plasticiser, it could suck it up on contact — all the plasticiser has to do is leave the inner insulator under elevated temperature conditions and move between the ground wires. This would even be probable, if the plasticiser here behaves in a similar way to the older phthalates. It would explain why the outer sheath softens at the onset of the problem. [3]

To date I’ve had four adaptors for this MacBook:
- Nº1: The first was a T-type tip. It did not have this problem — its problem (which I expect the new cable type is intended to fix) was sheath shrinkage, and detachment and fraying of the exposed ground wire. (Neither seem to have been properly secured inside the adaptor. But others found the sheath shrinking at the MagSafe end.) This became visible inside a year but it wasn’t too significant until year 3 (by which time it had begun to be a connectivity problem). Apple replaced it under warranty.
Nº2: The replacement had an L-tip and the newer type of sheath. The tip came off after about six months.
- Nº3: Not having time to try a fix, I got a cheap knock-off copy with a perfectly good cable and a MagSafe T-tip, but again the tip came off after about six months.
- Nº2 again: It had sat in a drawer meanwhile. (Now about a year old.) I resoldered the tip and returned it to use. After a few months the cable began to yellow, then developed green spots, and at about a year on, started to split. (Details in “A Disturbing Shade of Green”, originally written at that point.) I taped up the last six inches or so of cable, and awaited funds. That had to do for about another 17 months, by the end of which time the problem was creeping further up the cable, but as a stain with neither wrinkles nor cracks at that point. (Then the MacBook’s GPU went and the whole thing was out of action for a bit.)
- Nº4: The latest, bought in August 2013 and brought into use with the laptop (GPU replaced) in September. From brand new to the sheath splitting, in almost daily use for the last ten months, it has lasted about 50 weeks.
Unlike my recent experience with an expanded battery, I am not pleased with the failure mode of this (expensive) Apple product. This problem is not contained adequately or safely, and it occurs far too early.
The Progress of Nº2
For nearly a year, Adaptor Nº2 has been sat out of the way on a shelf in a cool, dry, low-light area, and although it has not been subject to operating levels of heat in this time, the cable has continued to degrade. (See note 4 for a possible mechanism.) It is now past four years old, and this is how it looks:
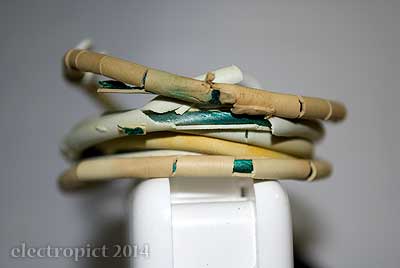
The yellowing has become browning — which happens eventually with boron migration in plastics, but not usually this fast. Areas of sheath which are not particularly yellowed have fragmented anyway.
At one point — before I got my camera fixed — there were actually slight drips of plasticiser forming at the lower side of the cable loops. I assume it mostly evaporates. The sheath has cracked, to the point where pieces are falling off when it’s moved. Clearly now the plasticiser has drained out, the remaining plastic is shrinking again, and has lost its plasticity — it might as well be stale bread for all the good it’s doing as an insulator. The adaptor was shelved on its side, with the cable in free air to avoid the green gunk touching anything. The cracking is visibly worse on the upper side, as the plasticiser drained downwards. How poor a plastic does this have to be, that gravity alone can cause (or continue) this kind of deterioration?
The black bit is the excessively large amount of self-amalgamating tape I wrapped round the original damage to extend its lifespan. It did better than expected. (A note for power connector designers: this big solid lump of tape actually made things easier, acting like a handle, as well as keeping the mechanical strain away from the normally fiddly little MagSafe tip. It hasn’t come off a second time, and I don’t think that means I’m so much better a solderist than Apple’s staff.)
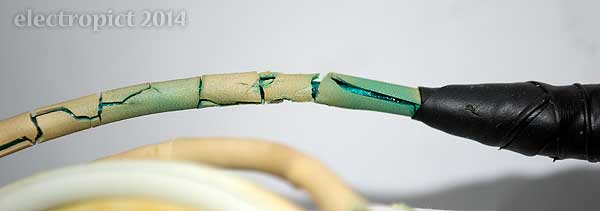
Reflections
So, my conclusion regarding MacBooks is that,
- I was right to think that a metal-bodied MacBook Pro would outlast the plastic-bodied iBook I had before it — at seven years old, apart from a replacement GPU [4] and some wear and tear on the plastic trim, it’s doing fine, and it’s even kept me warm in Winter; but
- recent Apple power supply cables (though not the adaptors themselves) are intolerable.
Contrast this with my 1993 PowerBook 145b power supply — chunky and ugly by comparison, to be sure — but no visible cable deterioration at all, and still delivering within 3% of its rated output after 21 years. What went wrong . . . ?
. . . and though technically it should still be under warranty for a few days yet, in what sense is it worth even trying to ask Apple for yet another new one which will end up the same? I have two Apple and one third-party MagSafe adaptors, and three tips, able to be fitted with a more reliable cable of my choice.
Plans
- Trim about two inches of sheath off the cable on Nº4. Self-amalgamating tape again — should get a last few weeks from it before the damage spreads.
- Revive Nº3 — it only needs the MagSafe tip resoldered. This may be difficult; I haven’t tried to fix a T-type tip before. No guarantees.
- Whether or not (2) is successful, open up Nº2 and replace the whole cable. I did look for something similar in the way of coaxial cable last year, unsuccessfully. But I suspect this isn’t necessary; it’s just a DC power supply. Ordinary 2-core flex should do — though all things considered I think I’ll opt for heat-resistant. Ideally this should include putting a socket in the adaptor, so the cable can be replaced if need be. This will probably not look very elegant . . . but nor does it in its existing state.
- If outcome good after suitable assessment period, repeat (3) for Nº4.
- As the MacBook isn’t going to last indefinitely either, save up for an all-Linux laptop with a sensible power supply. Assuming such things exist. Something solid, and repairable, like our desktop CPUs used to be. [5]
I suppose an alternative to (3/4) would just be to strip off the whole sheath and replace with heatshrink — but this isn’t really appealing; chances are that what we see on the outer sheath is also occurring in the inner sheath. The cables are simply not reliably safe.
To be continued . . .
This post has been updated in MagSafe As It Should Have Been.
Comment or Question about this page? write
Notes
- “MagSafe” is a trademark of Apple Europe and Apple globally I think, and basically I’ve reached the point where they can keep it. At least, it’s still a good idea, just badly implemented, like many proprietary technologies. ↖
- I don’t actually know they didn’t, but, you know, I’d have expected a dry mineral powder or something. ↖
The problem of migration of plasticiser from high concentrations in electrical insulators to areas of low concentrations in other materials is well known. This is why PVC sheathed cables should not be left in permanent contact with plastic thermal insulation. I am aware of no reason why the same would not be true between electrical insulators with differing concentrations.
Or, if the plasticiser behaves in the same way as oils and waxes, from insulators with lighter (smaller molecule) plasticisers to insulators with heavier (larger molecule) plasticisers of a similar type. In which case the larger more stable molecules could be partially dissolved and replaced by the lighter plasticiser (causing expansion), followed by hardening and shrinkage of the heavy-plasticiser insulator once the mixed solution drains out. Which seems to be exactly what happened to Adaptor Nº2 — its cable continued to degrade long after it was removed from any heat source. But I am far from being a materials chemist. ↖
- It may be worth noting that the pattern of GPU failures on these (and other manufacturer’s) products occurred because the ‘cold solder’ used had a tendency to reflow somewhere above 70°C. Clearly I had that kind of temperature going — or higher. Coincidentally, 70°C is the melting point of ordinary PVC insulators. (Softening and migration of plasticisers begins at lower temperatures even with conventional PVC/phthalate compounds and becomes problematic with protracted exposure.) Actually the MacBook has always tended to get too hot to touch in some areas under heavy processing load. And the MagSafe tip gets very uncomfortable to touch under heavy use and simultaneous recharging. ↖
- At least one reader is likely to want to persuade me of pads again. OK — though I’d like a pad that can run a proper OS, and handle a good text editor, plus Inkscape and the GIMP or similar. It must have a reasonable screen size, it must be able to communicate with a decent keyboard, and the keyboard must be modifiable. It sort of sounds like a laptop. But you know, why shouldn’t a laptop be modular? ↖
References
- See e.g.:
- ⟨www.basec.org.uk/News/Basec-News/Ask-BASEC-Technical [dead link]⟩,
- www.voltimum.co.uk/articles/green-goo-0 ↖
Article text ©2014 Electropict .
Click images for individual licences.